Technology Research center for the continuous process of renewal and technological improvement.
Over the last few years, TEKNOX has continued the process of renewal and technological improvement.
Innovations include:
DRYING
The redesign of the hot air drying system installed on some models has enabled the operating temperature, and therefore the overall energy consumption, to be reduced and performance to be increased by 30%.
CENTRIFUGAL CONDENSER
The new centrifugal condensation system, specially designed and patented by TEKNOX for water-based washing systems, has enabled the amount of steam that is generated to be significantly reduced and therefore also the cost of condensation equipment.
Technologic Innovations: THE ELECTRICAL PANEL DGT V4
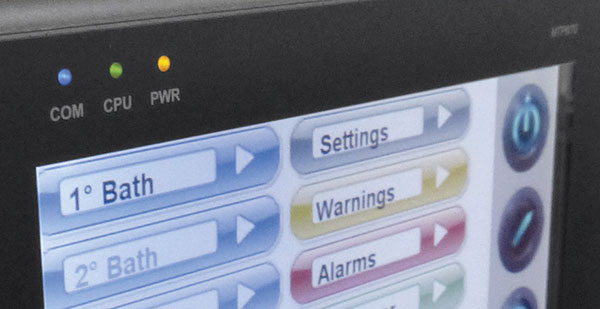
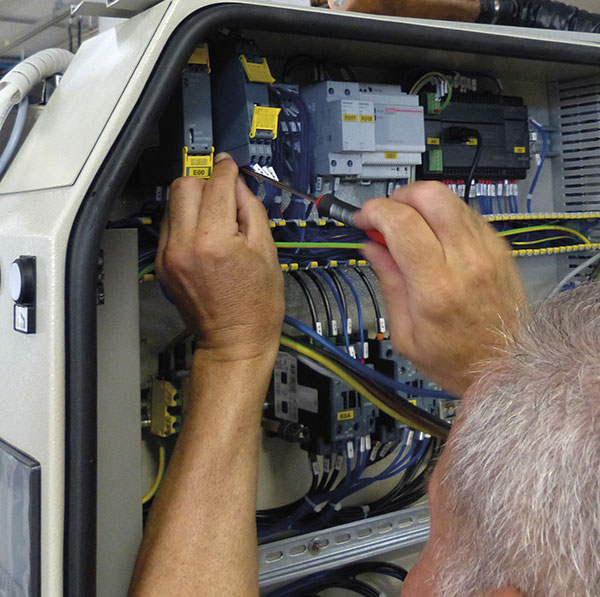
The new DGT V4 control system, which is standard on TEKNOX models, is composed of:
- a PLC that manages the input and output signals and controls the activation of heating resistances and motors
- a touch-screen operator panel with a 4.3” or 7” backlit TFT LCD, 65536 colours display
- Siemens electromechanical components
The control software enables you to:
- customize the main machine functions such as times, temperatures and work cycles
- define up to 16 operating programs, each of which can include up to 48 different stages (apart from continuous operation systems) via an easy to use graphical system
- check the status of the various components of the machine in real time via a mimic diagram display
- set up the weekly schedule to turn on the heating of the treatment fluids
- set up the weekly schedule to turn on the oil separator (if installed)
- set the language in which to display information
- manage the minimum, maximum and safety temperatures for the liquids
- manage warning signals and machine alarms
- obtain information regarding the total machine cycle time (hour meter, cycle counter)
- automatically manage maintenance
- enable advanced functions such as energy saving (to optimise the overall power consumption of the machine)