Parts washers catalog 3D LINE
Dyeing capacity (L x P x H) | Loading weight | Main tank | |
3D WAVE | Basket 30 x 45 x H30 cm | 50 kg | 160 lt |
---|
ADDITIVE DYEING SYSTEM - Plant for automatic dyeing in additive manufacturing
Specifically designed for the dyeing of 3D printed parts, the new 3DWAVE machine is the ideal solution to obtain exceptional results and maximise productivity.
The innovative immersion dyeing system guarantees precision and even colour.
3DWAVE is the perfect ally for companies that work with 3D technology and need an efficient, reliable machine.
ADVANTAGES
- ALL-IN-ONE: pre-rinsing – dyeing – rinsing – hot drying
- OPTIMAL DYEING OF COMPLEX SURFACES: thanks to the Rotowave system
- LOW OPERATING COSTS: energy consumption, dyeing and disposal
- HIGH PRODUCTIVITY: 1 complete cycle in less than 60 minutes
- WORKPIECE HOLDER: with lid for partial filling
EFFICIENCY… AND MORE
- EASY TO USE: automatic process, no intermediate handling
- CUSTOMISABLE PROGRAMS: that can easily be created according to individual needs
- TOWARDS INDUSTRY 5.0: 3DWAVE analyses and stores daily electricity consumption, thus allowing for energy saving and optimisation
The 3D WAVE project, patent pending 2023, is the result of a collaboration between two long-established Italian companies TEKNOX & NORBLAST that have combined their experience and expertise to offer an innovative opportunity for additive manufacturing professionals.
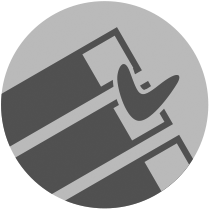
- HT (heating up to 80° C)
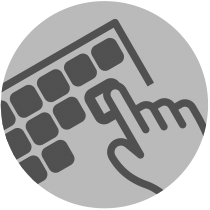
- PLC with color Touch Screen
- Industry 4.0 option
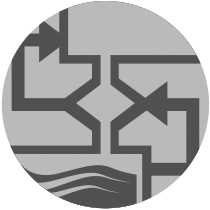
- Unique tank
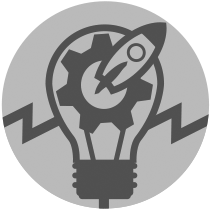
- Additive manufacturing
Video
PROCESS
The pieces are inserted into a stainless steel basket. The basket is equipped with a locking system at different heights that keeps the pieces inside and ensures they are not damaged during rotation.
Thanks to the RotoWave technology, which uses a partial immersion and continuous exchange system, the liquid is constantly in movement, allowing it to enter even the deepest recesses, improving the capacity of the dye to adhere to the surfaces, avoiding stagnation and streaking.
Thanks to the flexibility offered for the creation of customisable programs, the machine is able to operate automatically, with no intermediate handling.
- AUTOMATIC PRELIMINARY RINSE to remove any impurities on the surface
- DYEING OF PIECES USING ROTOWAVE TECHNOLOGY with slow rotation and partial immersion
- AUTOMATIC FINAL RINSE to remove any excess dye
- HOT AIR DRYING in a micro-filtered, temperature-controlled environment
Dimensions of workpiece holder | 450 x 300 x H 300 mm – mesh 12 x 12 mm |
Production volume per cycle | Up to full build HP Jet Fusion 5200 |
Cycle time | 30-60 minutes (based on the program phases activated) |
Pre-rinse and post-rinse | Integrated into the treatment cycle |
Heated air drying | Integrated into the treatment cycle |
Liquid working temperature | 60 °C – 80 °C |
Liquid dye percentage | 10% in water |
Tank capacity | 160 lt |
External dimensions of machine | W 1300 x D 960 x H 1200 |
Weight | ~ 260 kg |
Electricity supply | 3 PH 400 V 50 HZ + N + PE, total power 7 kW |
Water supply | Pressurised mains water; softened water recommended |
Compressed air | Pressure 6 bar - Flow 20 Nmc/h |
STANDARD FEATURES
- Maximum liquid level control in the tank and filling solenoid valve
- Automatic dye dispenser
- Water mains rinse and non-returnable drain
- Tank emptying pump
- Stainless steel box 471 x 321 x H300 mesh 12x12 mm with lid
- 4" colour touchscreen display for settings and programmes
- Industry 4.0 ready for Weintek HMI
- Automatic calculation of power consumption in real time
- Assisted lid closure with gas springs and hook closure
- Siemens power electrical components
- Aisi 304 stainless steel filter on pump suction
- Edge gasket
- Structure and plates in contact with the liquid in Aisi 304 stainless steel
- Minimum level control
- Safety limit switch on lid opening
- Gear motor for basket rotation with torque limiter and centring sensor
- Stainless steel electric pump with special seals
- Weekly programming of heating and oil separator ignition (if installed)
- IP55 electrical system, management with touchscreen PLC (DGT V4)
- Liquid heating with stainless steel heating element
- Bleaching of internal and external welds
- Flexible pump suction and delivery pipes (easy maintenance)
- Drain valves for tank emptying
- Manual valve for water filling
The turtle model was created by Ferocar. It is reproduced here without modifications, and distributed under the Creative Commons Attribution license https://creativecommons.org/licenses/by/4.0/deed.it, downloadable from https://www.thingiverse.com/thing:3753213
- 1000 litre tank with piping and connection fittings to collect waste water
- Single-column demineraliser with interchangeable resins and digital conductivity meter
- BLACK TCN base dye in 10-litre canisters